Points clés à retenir :
- Qu’est-ce que le lead time ? Le lead time est la durée entre le début et la fin d'un processus, notamment dans le secteur de la production et en gestion de projet.
- En quoi le lead time est-il différent du cycle time ? Le lead time englobe la durée totale du processus, tandis que le temps de cycle mesure le temps nécessaire pour accomplir une tâche spécifique au sein de ce processus.
- Comment calculer le lead time ? Le lead time peut être déterminé par des formules incluant les dates de livraison de commande, le temps de production, l'approvisionnement et les délais d'expédition, adaptés à des secteurs spécifiques.
- Quelles stratégies peuvent minimiser le lead time ? L'optimisation de la chaîne d'approvisionnement, la gestion des relations avec les fournisseurs, l'identification des dépendances et l'automatisation des processus peuvent contribuer à rationaliser les lead times.
- Pourquoi est-il important de calculer un lead time avec précision ? Des calculs précis du lead time aident à optimiser la planification et l'allocation des ressources, et à définir des attentes réalistes avec les parties prenantes, évitant ainsi les retards.
Le lead time est l'un des indicateurs les plus importants dans les opérations commerciales, mais il est souvent mal compris. Il influe sur la vitesse à laquelle les équipes peuvent répondre aux demandes, s'adapter au changement et assurer le bon fonctionnement des processus métiers. Lorsque le lead time est trop long ou imprévisible, il devient plus difficile de gérer efficacement les ressources ou de maintenir la satisfaction des clients.
Ce guide explique ce que signifie le lead time, comment le mesurer et les stratégies visant à le réduire dans différents secteurs.
Qu’est-ce que le lead time ?
Le lead time désigne le temps total requis pour mener à bien un processus, depuis la demande initiale jusqu'à la livraison finale. Il commence lorsqu'une commande est passée ou qu'une tâche est initiée, et se termine lorsque le livrable est fourni ou réalisé.
Dans les opérations commerciales, le lead time est utilisé pour suivre et gérer la durée des workflows clés. Cela peut inclure l'approvisionnement en matières premières, la réalisation du processus de production et la livraison des produits finis. Dans la chaîne d'approvisionnement et les achats, cela représente le délai entre l'établissement d'un bon de commande et la réception des marchandises.
Quelle est l’importance du lead time ?
La réduction du lead time a un impact direct et mesurable sur les processus métiers, la rentabilité et la satisfaction des clients. Vous trouverez ci-dessous les principales raisons pour lesquelles le lead time est important pour toutes les fonctions de l'entreprise :
Améliorer la planification et l'élaboration du calendrier
Une visibilité claire à chaque étape du lead time permet aux équipes de créer des calendriers de projet plus précis et d'allouer les ressources efficacement. Cela est particulièrement important dans la gestion de projet, où l'alignement des tâches sur des attentes réalistes permet d'éviter les dépassements budgétaires et les retards.
Améliorer la satisfaction des clients
Une livraison fiable et rapide améliore la satisfaction des clients en répondant à leurs attentes sans retards ni excuses. Lorsqu'un client passe une commande, il s'attend à une date de livraison précise.
Renforcer la gestion des stocks
Un lead time précis permet de prendre de meilleures décisions en matière de niveau de stock et réduit le risque de surstockage ou de rupture de stock. Il permet une gestion des stocks proactive en veillant à ce que les cycles de réapprovisionnement correspondent aux tendances d'utilisation et de demande, en particulier lors de la gestion des matières premières importantes.
Augmenter l'efficacité de la production
Un lead time long ou imprévisible peut perturber le processus de production et prolonger inutilement le temps de production. En mesurant et en surveillant chaque phase de la production, les équipes peuvent identifier les retards et réduire le lead time tout au long du cycle.
Minimiser les coûts liés aux retards
Chaque retard dans la chaîne d'approvisionnement augmente les frais généraux, immobilise le capital et limite la flexibilité. Des retards d'approvisionnement imprévus ou des délais d'approvisionnement prolongés peuvent bloquer les opérations et entraîner des temps d'arrêt coûteux. La gestion de l'intégralité du lead time permet aux entreprises de réagir plus rapidement et d'éviter les répercussions des retards de production.
Renforcer l'avantage concurrentiel
Un lead time de production plus rapide et des opérations rationalisées permettent aux entreprises de répondre rapidement aux demandes du marché. Un lead time cumulatif plus court se traduit souvent par des volumes de commandes plus élevés, donnant à l'entreprise un avantage sur ses concurrents qui ont des cycles d'exécution plus lents.
Composants du lead time
Le lead time est composé de différentes étapes. Comprendre les différents éléments qui constituent le lead time permet aux équipes d'identifier les processus complexes et les domaines d'amélioration possibles. Bien que la répartition exacte varie selon les industries, voici les principaux composants du lead time.
Composant | Description |
Temps de prétraitement | Temps passé à préparer les matériaux, les plans ou les intrants avant le début du travail |
Lead time de traitement |
Temps activement passé à produire, servir ou exécuter une tâche |
Temps de post-traitement | Temps requis après l'achèvement du travail, y compris l'emballage, les tests ou les approbations |
Temps d'approvisionnement | Temps nécessaire pour sourcer et recevoir des matières premières ou des fournitures |
Temps d'expédition | Temps nécessaire pour livrer le produit final au client ou à l'utilisateur final |
Temps d'attente | Temps d'inactivité entre les étapes, souvent dû aux files d'attente, aux approbations ou aux contraintes de ressources |
Lead time de commande demandée | La période de temps que le client s'attend à ce que la commande soit exécutée |
Lead time de commande réelle | Le temps réel écoulé depuis la passation de la commande jusqu'à la livraison |
Types de lead time
Différents types de lead time capturent différentes parties du processus de commande et de livraison. Identifier les types de lead time procure aux équipes un meilleur contrôle et un pouvoir de décision. Voici une répartition des types les plus courants.
Lead time client
Le lead time client est le temps total entre le moment où un client passe une commande et la livraison du produit ou service. Cela inclut toutes les étapes de traitement interne, de fabrication, d'emballage et d'expédition jusqu'au point de livraison.
Lead time matériel
Le lead time matériel désigne le temps nécessaire pour acquérir toutes les matières premières nécessaires auprès des fournisseurs externes. Cela commence dès qu'une commande d'achat est soumise à un fournisseur et se termine lorsque les matériaux sont reçus et prêts à l'utilisation.
Lead time de production
Il couvre la période nécessaire pour compléter le processus de production une fois que tous les matériaux sont disponibles. Cela commence lorsque la fabrication est programmée et continue jusqu'à ce que les produits finis soient prêts pour l'expédition.
Lead time cumulatif
Le lead time cumulatif est le temps total nécessaire pour réaliser un produit ou un service de A à Z, en supposant qu'aucun matériel n'est disponible. C'est souvent utilisé dans la gestion de la chaîne d'approvisionnement pour évaluer le temps de planification nécessaire pour répondre à une nouvelle commande à partir de zéro.
Lead time de livraison
Le lead time de livraison commence lorsque le produit quitte l'installation et se termine chez le client. Cela inclut le temps d'expédition, le dédouanement potentiel et la manutention finale. Il est particulièrement important dans la logistique mondiale et la livraison du dernier kilomètre.
Voici une répartition qui compare les différents types de lead time :
Type de lead time | Point de départ | Point final | Contrôlé par | Domaine |
Temps de superposition des tâches client | Reçoit la commande | Livre le produit au client | Fournisseur et transporteur | Ventes et réalisation |
Temps de superposition des tâches des matériaux | Envoie le bon de commande | Reçoit le matériel | Fournisseur | Approvisionnement et sourcing |
Temps de superposition des tâches de production | Matériaux disponibles | Produit prêt pour l'expédition | Équipes internes | Opérations de fabrication |
Temps de superposition cumulé | Pas de matériel disponible | Complète le produit | Équipes internes + externes | Chaîne d'approvisionnement |
Temps de superposition des tâches de livraison | Expédition depuis l'entrepôt | Arrivée à l'emplacement du client | Fournisseurs logistiques | Distribution et expédition |
Comment calculer le temps de superposition des tâches
Le temps de superposition des tâches est le plus utile lorsqu'il est mesuré avec précision . Les entreprises qui prennent le temps de le calculer correctement peuvent optimiser les processus et réduire les stocks excédentaires. Ci-dessous se trouve une répartition sur la façon d'aborder le calcul du temps de superposition des tâches, la formule standard et un exemple de son fonctionnement dans les opérations commerciales.
Calculateur de temps de superposition des tâches
Un calculateur de temps de superposition des tâches aide à automatiser et standardiser la mesure du temps entre l'entrée et la livraison. Il est utile dans les systèmes impliquant plusieurs fournisseurs ou étapes dans le processus de fabrication.
Logiciel de gestion de projet comprend souvent des calculateurs de temps de superposition des tâches qui suivent quand un client passe commande et quand le produit final est expédié. Ces calculateurs incluent souvent des données historiques telles que le temps de cycle et date de livraison. Cette visibilité permet aux équipes d'améliorer la prise de décisions et de réduire le temps de superposition des tâches dans les unités commerciales. Pour utiliser ces outils efficacement, il est important de comprendre la formule de base des calculs de temps de superposition.
Formule du temps de superposition des tâches
Ramakrishna Baliwada, Warehouse & Inventory Manager, shared on LinkedIn :
"Pour utiliser l'analyse des temps de superposition des tâches efficacement pour la gestion des stocks, commencez par mesurer combien de temps il faut entre la commande et la réception des marchandises. Utilisez ces informations pour définir des niveaux de stock de sécurité appropriés, garantissant ainsi d'avoir suffisamment de stock pour couvrir les retards."
Ainsi, la formule de temps de superposition des tâches la plus courante, qui est la suivante :
Temps de superposition (TS) = Date de livraison de la commande - Date de demande de la commande
Ce calcul peut s'appliquer dans différents contextes, y compris la fabrication, le développement de logiciels et la gestion de la chaîne d'approvisionnement. Dans des flux de travail plus complexes, la formule de temps de superposition peut incorporer d'autres éléments plus nuancés du processus de fabrication. En voici quelques autres exemples :
TS = Temps de fabrication + temps d'achat + temps d'expédition
- (Utilisé le plus souvent par les fabricants responsables de la production de produits)
TS = Temps d'achat + temps d'expédition
- (Utilisé le plus souvent par les détaillants responsables de l'obtention et de la livraison des produits)
Les équations ci-dessus utilisent l'approche de base consistant à prendre chaque partie du processus et simplement les additionner .
Exemple de calcul du temps de superposition des tâches
Ci-dessous un exemple simplifié de comment calculer le temps de superposition des tâches pour une entreprise de fabrication.
Scénario : Une entreprise reçoit une commande le 1er juin. Voici comment se déroule le calendrier :
Étape | Description | Date | Temps écoulé |
Reçoit la commande | Le client passe une commande | 1er Juin | — |
Commandes de matières premières | Le fournisseur confirme la disponibilité des matériaux | 2 juin | 1 jour |
Livre les matières premières | Reçoit tous les approvisionnements | 5 juin | 3 jours |
Le prétraitement commence | Début de la configuration et de la préparation | 6 juin | 1 jour |
Temps de traitement | Cycle de production | 7-9 juin | 3 jours |
Temps de post-traitement | Inspection, emballage, et approbations | 10 juin | 1 jour |
Temps d'expédition | Expédier les produits finis au client | 11-13 juin | 3 jours |
Dernière livraison | Complète et livre la commande | 13 juin | — |
Temps de superposition des tâches (LT) = 13 Juin – 1 Juin = 12 jours
Dans ce cas, le temps de superposition des tâches total est de 12 jours calendaires, couvrant chaque phase depuis la réception de la commande jusqu'à la livraison finale.
Facteurs influençant le temps de superposition des tâches
Le temps de superposition des tâches est influencé par de multiples facteurs internes et externes. En voici quelques-uns :
Performance des fournisseurs
Des envois tardifs, des niveaux d'inventaire bas ou des malentendus avec les fournisseurs peuvent allonger le temps de superposition des tâches d'un fournisseur. Même des retards mineurs d'approvisionnement peuvent affecter la disponibilité des matières premières, repoussant l'ensemble du calendrier.
Efficacité de la production
Un processus de production lent ou irrégulier augmente le temps de superposition des tâches de fabrication. Cela entraîne une manipulation manuelle, ce qui prolonge le temps de traitement nécessaire pour produire des biens ou des services.
Temps d'arrêt des équipements et des systèmes
Les temps d'arrêt inattendus des machines ou les pannes de systèmes peuvent arrêter complètement les opérations, retarder les commandes et perturber le processus de fabrication.
Disponibilité de l'inventaire
Un stock insuffisant ou une mauvaise gestion d'inventaire entraîne des retards en attendant le réapprovisionnement. Par exemple, un rapport Deloitte 2024 montre que le temps de superposition moyen des tâches pour les matériaux de production était de 79 jours en avril 2024. Cela représente une amélioration par rapport au pic de 100 jours en juillet 2022, mais reste au-dessus des niveaux pré-pandémiques, qui tournaient autour de 65 jours en 2019. Les données renforcent l'idée que les retards persistants dans la disponibilité des matériaux peuvent continuer à affecter l'efficacité de la production malgré les efforts de reprise.
Coordination de projet
Une mauvaise communication ou un manque d'alignement entre les équipes provoque des interruptions dans les transferts, notamment en gestion de projet. Des rôles peu clairs, des échéances manquées ou une visibilité limitée ajoutent un temps d'attente non nécessaire à travers les tâches.
Perturbations externes
Des événements comme des catastrophes naturelles, des grèves de transport ou une instabilité géopolitique peuvent provoquer des retards dans le temps de superposition des tâches de la chaîne d'approvisionnement. Les retards de transport à l'échelle mondiale peuvent s'étendre jusqu'à 20 jours en raison des instabilités géopolitiques en cours, affectant les délais de livraison et de superposition des tâches.
Le temps de superposition des tâches selon les différents secteurs
Le temps de superposition des tâches joue différents rôles selon le secteur d'activité. Le tableau ci-dessous décrit son fonctionnement dans les principaux domaines opérationnels et son importance.
Secteur | Application | Importance |
Gestion des stocks | Surveille le temps nécessaire pour réapprovisionner le stock à partir du moment où un point de réapprovisionnement est déclenché. | Aide à prévenir les surstocks ou les ruptures en alignant les commandes des clients et les réassorts avec la demande. |
Chaîne d'approvisionnement | Mesure le temps total pour transférer les biens des fournisseurs aux clients finaux. | Soutient la planification, réduit les retards d'approvisionnement et améliore la fiabilité des livraisons. |
Gestion de projet |
Se réfère à la durée entre l'initiation et la fin des tâches ou des jalons. |
Permet une programmation précise, améliore l'allocation des ressources et limite les dépassements. |
Développement logiciel | Se réfère au temps écoulé entre la demande de fonctionnalité ou le rapport de bogue et le déploiement. |
Aide les équipes à gérer les tâches en backlog et à livrer efficacement des mises à jour aux utilisateurs finaux. |
Pourquoi réduire les temps de superposition des tâches est important
Réduire les temps de superposition des tâches élimine des processus inutiles dans les départements. Les entreprises qui réduisent constamment leurs temps de superposition des tâches obtiennent un meilleur contrôle sur les coûts, la production et la réactivité. Voici comment une réduction des temps de superposition des tâches peut influencer les indicateurs clés de performance (KPI) :
KPI | Long temps de superposition des tâches | Réduction des temps de superposition des tâches |
Précision de réalisation | Ajustements fréquents à la commande confirmée, plaintes client |
Meilleure concordance avec les promesses de livraison et taux d'erreur réduit |
Coûts d'opérations | Frais récurrents dus à des files d'attente plus longues, ressources inutilisées et temps passé | Flux de travail allégés avec moins de gaspillage et moins de reprises |
Niveaux d'inventaire | Coûts de conservation plus élevés en raison d'un excès d'inventaire |
Gestion de l'inventaire améliorée avec un roulement plus rapide |
Calendrier de production | Goulots d'étranglement fréquents pendant le temps de prétraitement et les transferts de responsabilité | Flux plus fluide avec moins de retards entre les tâches |
Contrôle qualité |
Reprises augmentées et pression sur le temps d'inspection de dernière minute |
Sorties plus prévisibles et moins de corrections en fin de processus |
7 stratégies pour réduire les temps de superposition des tâches
Réduire les temps de superposition des tâches signifie identifier les retards à la source et apporter des changements opérationnels qui mènent à des processus efficaces. Voici sept stratégies pour vous aider à réduire les temps de superposition des tâches :
1. Approuver à l'avance les matériaux fréquemment commandés
Configurez des approbations automatiques flux de travail pour les matériaux commandés de manière répétée. Par exemple, si le même grade de matières premières est utilisé chaque semaine, faites passer le bon de commande par une liste de fournisseurs pré-approuvés. Cela élimine les allers-retours et supprime les retards causés par l'attente de l'approbation des achats.
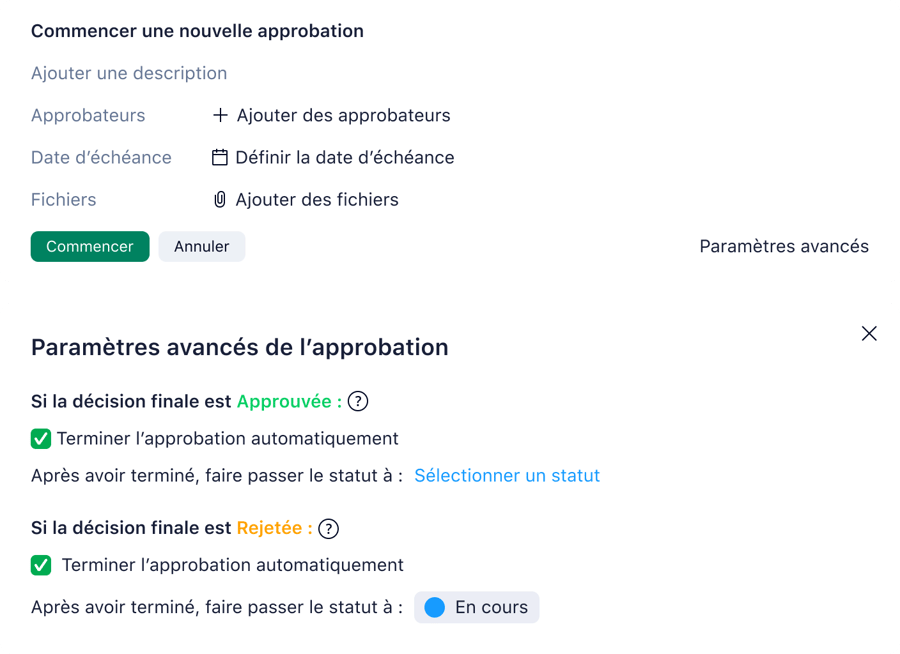
2. Créez une voie rapide pour les commandes en petits lots
Segmentez les commandes en fonction de leur complexité et de leur taille. Les commandes standard à faible volume doivent éviter les files d'attente de programmation complètes et passer par une ligne rapide dédiée. Cela évite d'encombrer le système avec de petites tâches qui pourraient être accomplies rapidement mais finissent par être retardées derrière des commandes complexes. Vous pouvez attribuer une machine spécifique ou un quart d'équipe par jour pour traiter uniquement les commandes expresses avec un délai d'exécution cible de 24–48 heures.
3. Établir des horaires de coupure clairs
De nombreuses entreprises reçoivent des commandes en continu tout au long de la journée, mais ne les traitent qu'une seule fois. Établissez et communiquez un horaire de coupure quotidien (par exemple, 14h00 heure locale), après lequel les commandes passent au jour suivant. Cela crée une cohérence et évite des temps d'attente inutiles causés par les fenêtres de lot manquées.
Astuce pro : Utilisez les journaux système pour identifier les pics de saisie de commande, puis définissez et testez des fenêtres de coupure qui équilibrent les charges de travail sans pousser la production vers des heures supplémentaires.
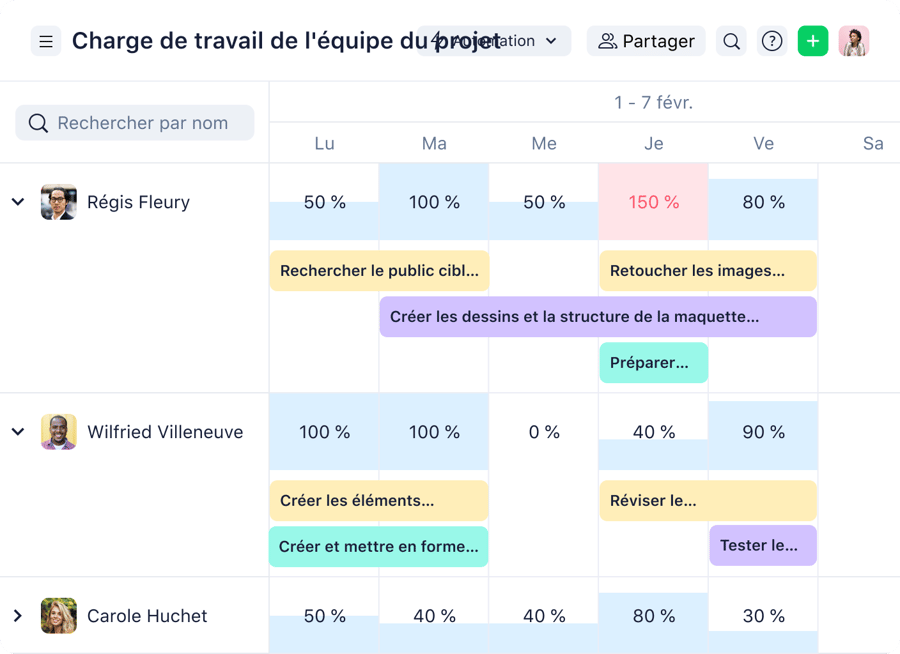
4. Former les opérateurs en polyvalence
Les temps de superposition des tâches augmentent souvent lorsqu'au moins un des opérateurs clés est indisponible. Au lieu d'arrêter la production ou de changer les priorités, formez les employés à utiliser plusieurs machines ou à gérer des tâches annexes. Cela réduit les dépendances et maintient la ligne en mouvement. Construisez une matrice de compétences par poste de travail et assignez au moins deux sauvegardes pour chaque processus clé. Révisez-le chaque mois lors des passages de quart.
5. Réorganisez la disposition du stockage
Un temps excessif se perd souvent simplement en se déplaçant entre le stockage et la ligne. Relocalisez les matériaux à forte utilisation pour être plus proches du point d'usage, réduisant ainsi le temps de traitement perdu en mouvement. Appliquez la même logique aux outils et aux matériaux d'emballage.
6. Révisez les tailles de lot et les déclencheurs de production
Des tailles de lot plus grandes peuvent retarder l'achèvement des commandes, notamment pour les productions multi-produits. Envisagez d'ajuster les tailles de lot en fonction de la fréquence de la demande et du temps de configuration. Des lots plus petits peuvent réduire l'inventaire inactif et améliorer le flux, surtout dans les environnements de fabrication avec de longs changements.
7. Renforcez les relations avec les fournisseurs
Maintenir des relations solides avec les fournisseurs clés aide à résoudre plus rapidement les problèmes lorsqu'ils surviennent. Des canaux de communication ouverts facilitent la confirmation de disponibilité, la négociation d'un délai d'exécution plus rapide, ou l'ajustement des priorités en cas de perturbations.
Comment Wrike vous aide à optimiser le temps de superposition des tâches
Réduire le temps de superposition des tâches implique de maîtriser chaque phase de travail avec les bons outils et processus de gestion de projet. Wrike soutient cela en donnant aux équipes la capacité de programmer, exécuter et surveiller chaque étape sur une plateforme centrale. Vous pouvez automatiser les tâches et éliminer les transmissions manuelles qui ralentissent les équipes.
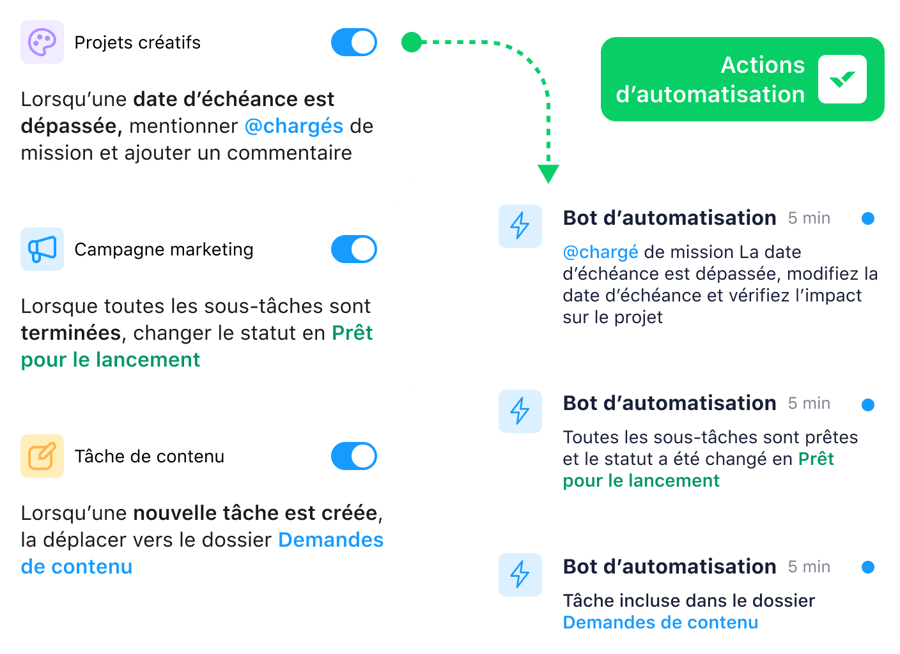
En tant que chef de projet supervisant les opérations dans la fabrication, la chaîne d'approvisionnement ou les achats, Wrike peut vous aider à gérer des tâches complexes de la début à la fin. Wrike offre des modèles préétablis et modèles de projet personnalisables qui réduisent le temps de configuration et garantissent la cohérence entre les flux de travail répétitifs.

Dans Wrike, nous créons des modèles de projet et des flux de travail de bout en bout pour s'adapter à la réalité des pays. Nous avons créé un modèle de projet flexible, où le projet reflète la taille et la complexité du projet client. Nous avons également personnalisé Wrike en fonction de quatre disciplines inhérentes aux bâtiments : le confort, la sécurité, la sécurité incendie et les services de performance énergétique.
Hannes Leitner, responsable de l’exécution de projets
Réduisez votre temps de superposition et délivrez des résultats plus prévisibles avec Wrike — commencez votre essai gratuit de deux semaines dès aujourd'hui.
FAQ
Qu'est-ce que le temps de superposition des tâches par rapport au temps de cycle ?
Le temps de superposition des tâches est le temps total entre la demande et la livraison du produit final. Le temps de cycle ne mesure que le temps passé activement à travailler sur la tâche ou la production.
Pourquoi le temps de superposition des tâches est-il important dans l'inventaire ?
Le temps de superposition des tâches influe sur le moment où le stock doit être réapprovisionné pour éviter les ruptures ou les surstocks. Des données précises sur le temps de superposition des tâches améliorent la gestion des stocks, soutiennent de meilleures prévisions, et réduisent les coûts de détention.
Comment puis-je réduire mon temps de superposition des tâches ?
Pour réduire le temps de superposition des tâches, éliminez les délais de processus, automatisez les étapes manuelles, standardisez les flux de travail, et améliorez la fiabilité des fournisseurs. Examinez chaque étape de votre flux de travail et adressez les lacunes qui ajoutent un temps inutile.
Nous vous remercions de l’intérêt que vous portez à notre e-book!
Téléchargez-le maintenantNous avons également envoyé le lien de l'eBook à votre e-mail pour votre commodité.