重要なポイント:
- リードタイムとは? リードタイムとは、プロセスの開始から完了までの期間であり、特に製造業やプロジェクト管理において重要です。
- リードタイムはサイクルタイムとどう違うのか? リードタイムはプロセス全体の期間を含むのに対し、サイクルタイムはそのプロセス内の特定のタスクを完了するのにかかる時間を計測します。
- リードタイムをどのように計算するのでしょうか? リードタイムは、注文の納期、製造時間、調達、輸送時間を含む業界ごとにカスタマイズされた計算式で決定できます。
- リードタイムを短縮するための戦略は何か? サプライチェーンを最適化し、サプライヤーとの関係を管理し、依存関係を特定し、プロセスを自動化することで、リードタイムを効率化できます。
- なぜ正確なリードタイムが重要なのか? 正確なリードタイム計算は、効果的な計画、リソースの配分、ステークホルダーとの現実的な期待設定に役立ち、遅延を避けます。
リードタイムはビジネスオペレーションにおいて最も重要なメトリクスの1つですが、よく誤解されます。 それは、チームがリクエストを迅速に履行し、変化に適応し、ビジネスプロセスを円滑に進行させる能力に影響を与えます。 リードタイムが長すぎたり予測不能な場合、リソース管理や顧客満足の維持が困難になります。
このガイドは、リードタイムの意味、測定方法、およびさまざまな業界でそれを短縮するための戦略を解説します。
リードタイムとは?
リードタイムは、プロセスを完了するまでの総時間を指し、最初のリクエストから最終的な納品までです。 注文が行われた際やタスクが開始された時から始まり、成果物が受け取られまたは完了する時点で終了します。
ビジネスオペレーションでは、リードタイムは重要なワークフローの期間を追跡し管理するために使用されます。 それには原材料の調達、製造プロセスの実行、完成品の納品が含まれる場合があります。 サプライチェーンや調達においては、発注を行ってから商品の受領までの時間をカバーします。
リードタイムの重要性とは?
リードタイムを短縮することは、ビジネスプロセス、利益性、顧客満足に直接かつ測定可能な影響を与えます。 以下は、ビジネスの機能全体にわたり、リードタイムが重要である理由の主要なものです:
プランニングとスケジューリングの改善
リードタイムの各ステージを明確に可視化することで、チームはより正確なプロジェクトスケジュールを作成し、リソースを効果的に配分できます。 これは、タスクを現実的な期待と合わせて調整し、オーバーランや遅延を避けるのに役立つプロジェクト管理において特に重要です。
顧客満足度の向上
信頼性が高く迅速な納品は、遅延や言い訳なしに期待に応えることで顧客満足度を向上させます。 顧客が注文を出すとき、正確な納品日を期待しています。
在庫管理の強化
正確なリードタイムは、より良い在庫レベルの決定をサポートし、過剰在庫や品切れのリスクを低減します。 それによりプロアクティブな 在庫管理 は特に重要な原材料を管理する際に、再在庫サイクルを使用量や需要の傾向と一致させて行うことができます。
生産効率の向上
長いまたは予測不可能なリードタイムは、製造プロセスを混乱させ、不必要に生産時間を延ばすことがあります。 生産の各フェーズを測定およびモニタリングすることで、チームは遅延を特定し、リードタイム全体を短縮できます。
遅延に関連するコストを最小化
サプライチェーンの遅延はすべて間接費を増やし、資本を拘束し、柔軟性を制限します。 予期しない供給の遅れや調達時間の延長は、オペレーションを停滞させ、高額なダウンタイムを招く可能性があります。 リードタイム全体の管理は、ビジネスが素早く対応し、遅延による波及効果を回避するのに役立ちます。
競争優位性の構築
製造リードタイムの短縮と効率化されたオペレーションにより、ビジネスは市場の需要に迅速に対応できます。 累積リードタイムが短くなると、一般に注文量が増加し、より遅い履行サイクルを持つ競合他社に対して競争力を持つ。
リードタイムの構成要素
リードタイムは異なるフェーズで成り立っています。 リードタイムを構成する各要素を理解することで、チームは複雑なプロセスを特定し、改善できる部分を明確にします。 業界によって正確な詳細は異なりますが、以下がリードタイムの主要な構成要素です。
コンポーネント | 説明 |
前処理時間 | 作業開始前に材料、プラン、またはインプットを準備するのに費やされる時間 |
処理リードタイム |
生産、サービス、またはタスクの実行に実際に費やされた時間 |
後処理時間 | 作業が完了した後に必要な時間(包装、テスト、または承認を含む) |
調達時間 | 原材料または供給品を調達し受け取るのに必要な時間 |
配送時間 | 最終製品を顧客またはエンドユーザーに届けるのにかかる時間 |
待ち時間 | ステージ間のアイドルタイム、しばしばキュー、承認、リソース制約による |
リクエストされた注文リードタイム | 顧客の期待する注文履行の期間 |
実際の注文リードタイム | 注文が行われてから納品されるまでにかかった実際の時間 |
リードタイムの種類
異なるリードタイムの種類は注文と納品プロセスの異なる部分を捉えます。 リードタイムの種類を特定することは、チームにより良い管理能力と意思決定力を与えます。 以下に最も一般的な種類の内訳があります。
カスタマーリードタイム
カスタマーリードタイムは、顧客が注文を出してから製品またはサービスが納品されるまでの総時間です。 これは納品時点までのすべての社内処理、製造、包装、および輸送のステップを含みます。
材料リードタイム
材料リードタイムは、外部の供給業者から必要なすべての原材料を取得するのにかかる時間を指します。 これは、ベンダーに発注書を送信する瞬間から始まり、材料が受け取られ、利用可能な状態になるまで続きます。
生産リードタイム
これは、すべての材料が入手可能になった後の生産プロセスを完了するために必要な期間をカバーします。 製造がスケジュールされ、完成品が出荷可能になるまで続きます。
累積リードタイム
累積リードタイムは、材料が手元にないことを前提に、製品またはサービスを開始から終了まで完了するために必要な総時間です。 これは、新規注文にゼロから対応するために必要な計画時間を評価するためにサプライチェーン管理で頻繁に使われます。
納品リードタイム
納品リードタイムは、製品が施設を出発して顧客の場所に到達するまでの時間です。 これは、配送時間、通関の可能性、最終的なハンドリングを含みます。 これは、特にグローバルロジスティクスやラストマイルデリバリーにおいて重要です。
以下は、異なるリードタイムのタイプを比較する内訳です:
リードタイムタイプ | 開始点 | 終了点 | によって制御される | ドメイン |
カスタマーリードタイム | 注文を受け取る | 顧客へのプロダクト配達 | どちらもサプライヤーと運送業者 | 販売とフルフィルメント |
資材リードタイム | 購買発注を送信する | 材料を受け取る | サプライヤー | 調達とソーシング |
生産リードタイム | 材料が利用可能 | 出荷の準備ができた製品 | 社内チーム | 製造オペレーション |
累計リードタイム | 材料が利用不可 | 製品を完了 | 社内および外部チーム | サプライチェーン |
配達リードタイム | 倉庫からの出荷 | 顧客先への到着 | 物流事業者 | 流通と配送 |
リードタイムを計算する方法
リードタイムは正確に測定されたときに最も役立ちます。 リードタイムを正確に計算する時間をかけている企業は、プロセスの最適化と過剰な在庫の削減が可能です。 以下に、リードタイムの計算方法、標準的な計算式、およびビジネスオペレーションにおける使用例の内訳を示します。
リードタイム計算機
リードタイム計算機は、入力から納品までの時間計測を自動化し、標準化します。 これは、複数のサプライヤーや製造工程の段階を含むシステムで役立ちます。
プロジェクト管理ソフトウェア には、顧客が注文をした時と最終製品が出荷された時を追跡するリードタイム計算機がしばしば含まれています。 これらの計算機はしばしば、 サイクルタイム 及び納品日などの履歴データを含んでいます。 この可視性により、チームは意思決定を改善し、ビジネスユニット全体でリードタイムを短縮することができます。 これらのツールを効果的に使用するには、リードタイム計算の基本的な公式を理解することが重要です。
リードタイム計算式
Ramakrishna Baliwada, ウェアハウス & インベントリーマネージャー、が共有しました:LinkedIn:
"リードタイム分析を効果的に在庫管理に使用するためには、注文を出してから商品を受け取るまでの時間を計測することから始めてください。 この情報を基に、適切な安全在庫レベルを設定し、遅延をカバーできるような在庫を確保してください。"
したがって、最も一般的なリードタイム公式は次のように言います:
リードタイム(LT)= 注文納品日 − 注文リクエスト日
この計算は、製造業、ソフトウェア開発、サプライチェーンマネジメントなどのさまざまなコンテキストで適用できます。 より複雑なワークフローでは、リードタイム公式は製造工程の他の、より微妙な部分を取り入れるかもしれません。 他のいくつかの例を以下に示します:
LT = 製造時間 + 調達時間 + 配送時間
- (最も一般的に製品を生産する責任者によって使用されます)
LT = 調達時間 + 配送時間
- (最も一般的に製品の調達と納品を担う小売業者によって使用されます)
上記のような方程式では、プロセスの各部分を取り込み、それらを単に足し合わせるという基本的なアプローチを使用します。。
リードタイム計算の例
以下は、製造会社のリードタイムの計算方法の簡略化された例です。
シナリオ:ある会社が6月1日に注文を受け取ります。 タイムラインは次のように展開されます:
ステップ | 説明 | 日付 | 経過時間 |
注文を受け取る | 顧客が注文をする | 6月1日 | — |
原材料を注文する | ベンダーが材料の利用可能性を確認する | 6月2日 | 1日 |
原材料を配達する | 全ての供給品を受け取る | 6月5日 | 3日 |
前処理が始まる | セットアップと準備開始 | 6月6日 | 1日 |
処理時間 | 生産実行 | 6月7-9日 | 3日 |
後処理時間 | 検査、パッケージング、および承認 | 6月10日 | 1日 |
配送時間 | 顧客に完了した製品を発送 | 6月11-13日 | 3日 |
最終納品 | 注文を完了し、納品 | 6月13日 | — |
リードタイム(LT)= 6月13日 – 6月1日 = 12日
この場合、総リードタイムは12日間で、受注から最終納品までの全フェーズをカバーします。
リードタイムに影響を与える要因
リードタイムは、多くの内部および外部要因によって影響を受けます。 これらの要因には次のものが含まれます:
サプライヤーパフォーマンス
遅れた出荷、在庫レベルの低下、ベンダーとのコミュニケーション不全は、サプライヤーのリードタイムを延ばすことがあります。 わずかな供給遅延でも原材料の入手可能性に影響を与え、全体のスケジュールを後退させる可能性があります。
生産効率
遅いまたは一貫性のない生産プロセスは、製造リードタイムを増加させます。 これにより手動処理が必要となり、商品やサービスを生産するのに必要な処理時間が延びます。
機械・システムのダウンタイム
予期しない機械のダウンタイムやシステムのアウトは運用を完全に停止させ、注文の遅れや製造プロセスの中断を引き起こします。
在庫の入手可能性
在庫不足または不適切な在庫管理がリプレニッシュメントを待つ間に遅れを引き起こします。 例えば、 デロイト2024年報告書 では、2024年4月に生産材料の平均リードタイムが79日だったことを示しています。 これは、2022年7月の100日間のピークからの改善を示していますが、パンデミック前の平均であった2019年の約65日を上回っています。 このデータは、材料の入手可能性における持続的な遅延がどのように製造効率に影響を与え続けるかを裏付けています。
プロジェクトの調整
チーム間のコミュニケーション不全や非整合は、特にプロジェクト管理の状況で、引き継ぎに混乱を引き起こします。 不明確な役割、締め切りの遅れ、視界の不十分さが不要な待ち時間をタスク全体で増やします。
外部の混乱
自然災害、運送ストライキ、地政学的な不安定さといったイベントは、サプライチェーンのリードタイムに遅れを引き起こす可能性があります。 世界の運送遅延 は、 20日間 まで延長する可能性があり、納期およびリードタイムに影響を与えます。
異なる業種におけるリードタイム
リードタイムは、業種に応じて異なる役割を担います。 以下のテーブルには、重要な運用領域における機能とその重要性が概説されています。
事業分野 | 適用 | 重要度 |
在庫管理 | 再注文ポイントがトリガーされてから在庫を補充するまでにかかる時間を追跡 | 顧客の注文と再注文を需要に合わせることで、過剰在庫や在庫切れを防ぐ |
サプライチェーン | 商品をサプライヤーから最終顧客に移動するまでの合計時間を測定 | 計画をサポートし、供給遅延を減少させ、納品の信頼性を向上する |
プロジェクト管理 |
タスクやマイルストーンの開始から完了までの期間を指す |
正確なスケジューリングを可能にし、リソース配分を改善し、オーバーランを制限する |
ソフトウェア開発 | フィーチャーのリクエストまたはバグレポートからデプロイメントまでの時間を指す |
チームがバックログを管理し、エンドユーザーに効率的にアップデートを届けるのを助ける |
リードタイムの短縮が重要な理由
リードタイムを短縮することで、部門全体で不要なプロセスを排除します。 リードタイムを一貫して短縮する企業は、コスト、成果物、対応力をより効果的に管理できます。 リードタイムの短縮が、主要業績評価指標(KPI)にどのように影響を与えるかを以下に示します:
KPI | 長いリードタイム | 短縮されたリードタイム |
フルフィルメントの正確性 | 確認済み注文への頻繁な調整、顧客の苦情 |
納期遵守とエラー率の低減の向上 |
運用コスト | 長い待ち行列、アイドルリソース、および実績時間のための持続的オーバーヘッド | 廃棄物を削減し、再制作が少ないリーンなワークフロー |
在庫レベル | 過剰在庫による保管コストの増加 |
回転が速い在庫管理の改善 |
生産スケジュール | 前処理時間や引き継ぎ中の頻繁なハブなど | タスク間の遅延が少ないスムーズな流れ |
品質管理 |
再制作や最後の検査時間のプレッシャーの増加 |
より予測可能な成果物と遅れたステージでの修正が少ない |
リードタイムを短縮するための7つの戦略
リードタイムを短縮するとは、遅延を生じる原因を特定し、効率的なプロセスを実現するための運用変更を行うことです。 以下は、リードタイムを短縮するための7つの戦略です:
1. 頻繁に注文される素材を事前に承認する
自動承認 ワークフローを設定し、繰り返し注文される素材に対応します。 例えば、同じグレードの原材料が毎週使用される場合、購買注文を事前承認されたベンダーリスト経由でルーティングします。 これにより、対話が無くなり、購入の承認を待つことで生じる遅延を排除します。
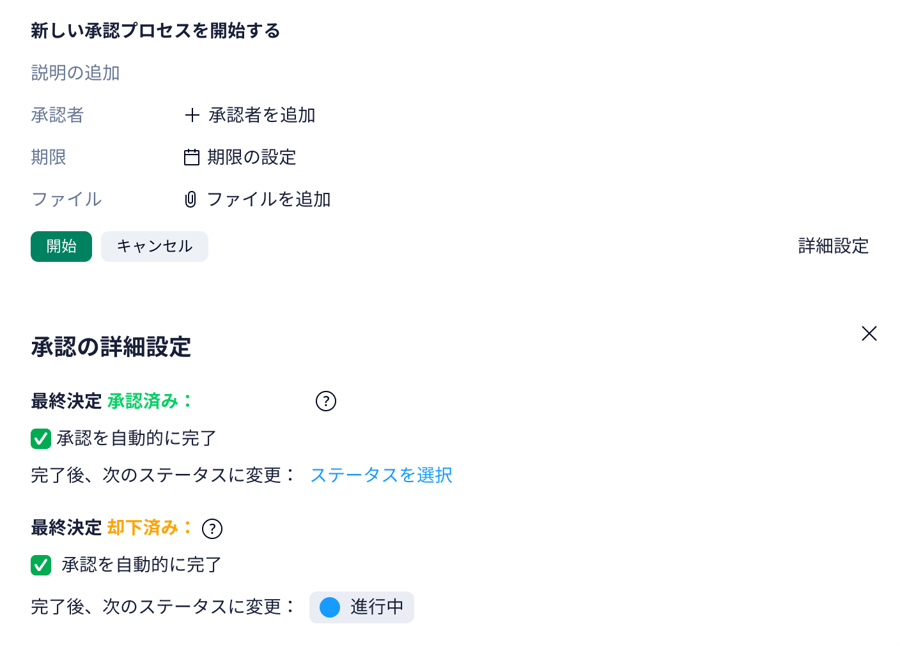
2. 小ロット注文用の優先ラインを作成する
注文を複雑さとサイズに基づいてセグメント化します。 少量の標準注文は、完全なスケジュール待ちを回避し、専用の優先ラインを経由する必要があります。 これにより、小さな作業が迅速に完了されるが、複雑な作業の後ろで遅れることを避けられます。 ファストトラック注文のみに対応するために、1日に特定の機械またはチームのシフトを割り当て、24~48時間を目標としたターンアラウンドを定めます。
3. 明確な締め切り時間を設定する
多くの企業が注文を1日中受け続けますが、それらを一回に処理します。 1日の締め切り時間(例:現地時間の午後2時)を設定し、コミュニケーションすることで、その後の注文は翌日にロールします。 これにより、一貫性が生まれ、バッチウインドウがミスされることによる不要な待ち時間を回避できます。
プロのヒント:システムログを使用して、注文エントリのピークパターンを特定し、 作業負荷を調整 するウインドウを定義し、テストして、残業に押し込まずに実行します。
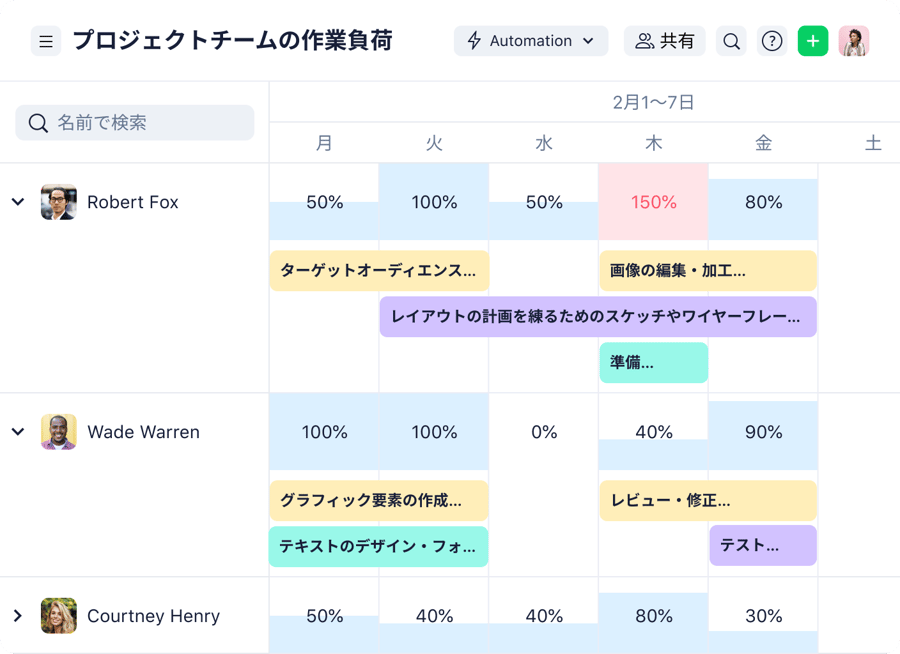
4. オペレーターをクロストレーニングする
主要なオペレーターが利用できない場合、リードタイムはしばしば増加します。 生産を停止したり優先順位をシフトしたりする代わりに、従業員をクロストレーニングして複数の機械を操作したり、隣接したタスクを管理したりするようにします。 これにより、依存関係を削減し、ラインを稼働させ続けます。 作業ステーションごとにスキルマトリックスを構築し、各重要プロセスに少なくとも2つのバックアップを指名します。 シフト交代期間中に毎月それを見直します。
5. ストレージレイアウトを再編成する
余計な時間は、しばしば保管場所とラインの間を移動するだけで失われます。 使用頻度の高い素材を使用先の近くに移動して、無駄な動作によって失われる処理時間を短縮します。 同じ論理をツールや包装材料にも適用します。
6. バッチサイズと生産トリガーをレビューする
大きなバッチサイズは、特に混合製品の実行において注文の完了を遅らせる可能性があります。 需要の頻度とセットアップ時間に基づいてバッチサイズを調整することを検討します。 特に長い変更に時間を要する製造環境では、バッチを小さくすることでアイドル在庫を減らし、フローを改善できるかもしれません。
7. サプライヤーとの関係を強化する
重要なサプライヤーとの強い関係を保つことは、問題が発生した際の迅速な解決に役立ちます。 オープンなコミュニケーションチャネルは、可用性の確認、早いターンアラウンドの交渉、もしくは混乱時の優先度の調整を容易にします。
Wrikeでリードタイムを最適化する方法
リードタイムを短縮するには、プロジェクト管理のツールとプロセスを使用して、作業の各段階を制御することが求められます。 Wrikeは、チームが一元化されたプラットフォームで計画し、実行し、各ステップを監視できる能力を提供してこれをサポートします。 可能なこと: タスクを自動化することと、チームの速度を落とす手作業の引き継ぎを排除します。
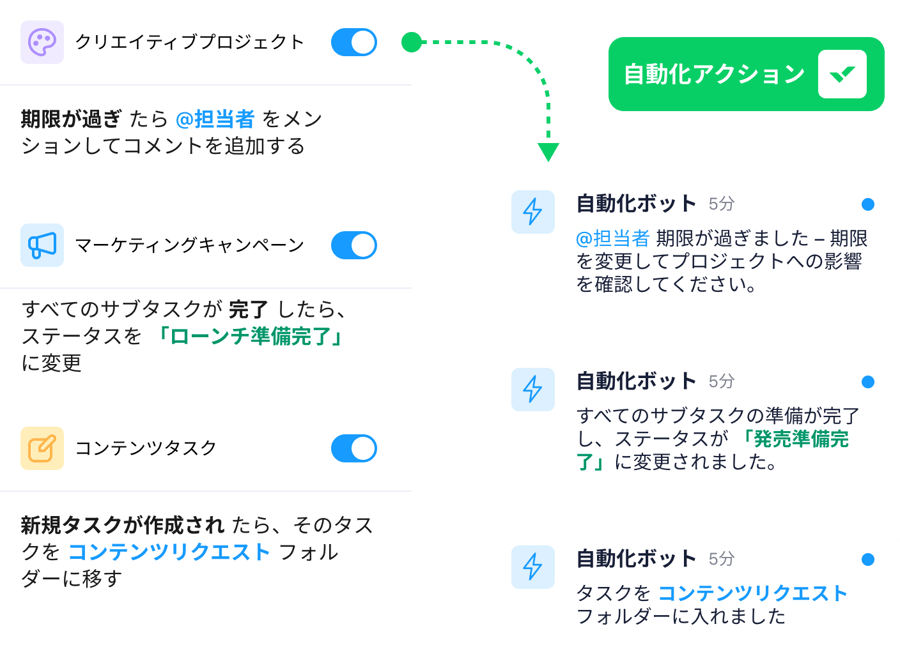
製造、サプライチェーン、または調達におけるオペレーションを監督するプロジェクトマネージャーとして、Wrikeは開始から終了まで複雑なタスクを管理するのに役立ちます。 Wrikeが提供するテンプレート カスタマイズ可能なプロジェクトテンプレートが、セットアップ時間を短縮し、繰り返し可能なワークフロー全体の一貫性を確保します。

Wrikeでは、プロジェクトテンプレートや端から端までのワークフローを作成して、国々の実情に合うように調整しています。プロジェクトの規模と顧客プロジェクトの複雑さに応じてフレキシブルなプロジェクトテンプレートを作成しました。 また、快適性、セキュリティ、火災安全、エネルギーパフォーマンスサービスという4つの異なる建築分野に合わせて、Wrikeをカスタマイズしました。
ハンネス・ライトナー氏(プロジェクト実行プロセスオーナー)
リードタイムを短縮して、Wrikeでより予測可能な結果を届けましょう— 2週間の無料トライアルを今すぐ始めましょう。
よくある質問
リードタイムとサイクルタイムとは?
リードタイムは、リクエストが行われてから出力が提供されるまでの全体の時間です。 サイクルタイムはタスクや生産に積極的に作業する際に費やされる時間のみを測ります。
在庫におけるリードタイムの重要性は何ですか?
リードタイムは、欠品や過剰在庫を避けるためにいつ在庫を再注文すべきかに影響します。 正確なリードタイムデータは、在庫管理を改善し、より良い予測をサポートし、保管コストを削減します。
リードタイムをどう短縮できますか?
リードタイムを短縮するには、プロセス遅延を排除し、手動のステップを自動化し、ワークフローを標準化し、サプライヤーの信頼性を向上させます。 ワークフローの各段階を見直し、不要な時間を加えるギャップに対処します。